
GET TO KNOW HITECH'S MILLING

Robots equipped with laser cutting and welding systems offer exceptional precision and accuracy (Usually the tolerance is the robot imperfection in precision). They can execute intricate cuts and welds with minimal heat-affected zones, resulting in high-quality, consistent outcomes.
This precision can be increased with a camera vision system. We can make the robot follow curvy lines or weld small micro seams.
These robotic systems are highly adaptable and can work with various materials, including metals, plastics, and composites. Their flexibility allows for the handling of diverse shapes and sizes, making them suitable for a wide range of industries and applications.
You can integrate additional axis for longer parts or round positioners for long tubes or cylindrical objects.
Robotic laser systems can operate 24/7, ensuring consistent and repeatable results. They eliminate the variability associated with manual labor, reducing the risk of errors and defects in the final products.
Laser cutting and welding robots are equipped with advanced safety features, including sensors and interlocks, to protect human operators from exposure to potentially harmful laser radiation. This makes them a safe and reliable choice for industrial manufacturing processes.
Laser cutting and welding robots work at impressive speeds, significantly improving production efficiency. Their continuous operation reduces downtime, leading to faster turnaround times and cost savings.


05
SAFETY
04
CONSISTENCY
03
VERSATILITY
02
SPEED AND EFFICIENCY
01
PRECISION AND ACCURACY

AUTOMATION SOLUTION
LASER CUTTING & WELDING
Raycus is a leading provider of laser welding and cutting solutions, renowned for its cutting-edge technology and high-performance laser systems. Raycus' laser welding and cutting technologies are sought after by businesses around the world due to precision, efficiency and their ability to enhance productivity and reduce operational costs.
We offer powerful and versatile systems that excel in welding and cutting a wide range of materials with exceptional speed and precision. Whether it's sheet metal, stainless steel, or other materials, Raycus laser cutting systems are capable of producing intricate and high-quality cuts for diverse industrial needs.

TECHNOLOGY
MILLING
Robotic arm milling is a versatile and cost-effective manufacturing process that offers flexibility and precision. It outperforms traditional CNC milling in adaptability, as robotic arms can handle various workpieces and complex milling tasks with ease, making it an ideal choice for diverse applications and smaller production runs.
Key advantage of robotic arm milling is the ability to perform complex and multi-axis milling tasks with ease. Robotic arms can access difficult-to-reach areas with linear tracks for example and perform tasks that might be challenging for traditional CNC machines. Additionally, robotic arm milling is often more cost-effective for small to medium-sized production runs.

GET TO KNOW RAYCUS LASER'S

Robots equipped for milling operations provide exceptional precision. Their multi-axis movement, often with six degrees of freedom, enables them to access complex geometries and execute highly accurate cuts. This level of precision is especially valuable in industries like aerospace and medical, where tight tolerances and intricate components are the norm.
Robotic milling is not limited to specific materials. These systems can efficiently work on various substrates, allowing manufacturers to explore new materials and experiment with different designs without significant retooling. This versatility opens up opportunities for innovation and product development.
Examples: Foam, carbon fiber, plastics, composites, hybrids, even some metals...
Robotic milling finds applications in various industries, such as automotive, aerospace, art and sculpture, mold making, and more. In automotive manufacturing, for instance, robots are used for trimming and finishing parts. In aerospace, they help produce complex components with high precision. The applications are virtually endless, showcasing the adaptability of robotic milling.
While CNC machines are highly capable and reliable, there are specific scenarios where robotic milling shines.
Robots are more adaptable to changing production needs, as they can be easily reprogrammed for new tasks.
They're also often more cost-effective for smaller production runs or prototyping, as they don't require expensive, dedicated CNC machines for each task.
The ability to switch between milling and other tasks, like welding or material handling, in the same robotic system further enhances their efficiency and value in modern manufacturing environments. Robots also offer the advantage of easy integration into existing automated production lines, providing a seamless, end-to-end manufacturing solution.
Robotic milling systems are incredibly versatile and flexible. They can handle a wide range of materials, including metals, plastics, composites, and even wood. Additionally, these systems can quickly adapt to different milling tools and tasks, making them suitable for diverse applications, from automotive prototyping to architectural modeling.
They can also be integrated with additional axis like linear tracks or rotating tables for different objects, like longer parts or 3D modeling.
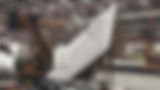

05
WHY A ROBOT, NOT CNC?
04
GENERAL USES
03
MATERIALS
02
VERSATILITY & FLEXIBILITY
01
PRECISION

AUTOMATION SOLUTION
AMR/AGV

GET TO KNOW DOBOT'S PALLETIZING
Introducing our cutting-edge plug and play collaborative robotic mini cell, the ultimate solution for seamless and rapid palletizing integration. Designed with simplicity and efficiency in mind, this innovative system enables businesses to effortlessly automate their palletizing processes.
With its user-friendly interface and straightforward setup, you can have this mini cell up and running in no time, eliminating the need for complex and time-consuming integration processes. Its intuitive programming allows users to easily teach the robot new palletizing tasks, making it a versatile addition to any production line.

GET TO KNOW MIG WELDING
Robotic welding solutions using MIG (Metal Inert Gas). With Fronius, we deliver precision and quality that meet the highest standards in welding, while Megmeet and Aotai bring innovation and cost-effective efficiency to your operations. Whether you're in automotive, aerospace, manufacturing, or any other industry.
Optimize your processes and boost productivity.
Discover the future of welding with Reprobots, where the expertise of Fronius, the innovation of Megmeet, and the accessibility of Aotai converge to drive your success. We understand that welding is at the heart of your production, and our goal is to ensure that you have the best tools and solutions at your disposal.

Youibot's Automated Mobile Robots (AMRs) represent a groundbreaking advancement in automation technology. These AMRs are a testament to innovation and efficiency in various industries. With their intelligent navigation systems, they effortlessly navigate through complex environments, making them invaluable assets for material handling, logistics, and manufacturing tasks.
The greatness of Youibot's AMRs lies in their adaptability and scalability. These robots can be easily integrated into existing workflows, reducing labor costs and streamlining operations. Whether in warehouses, factories, or hospitals, they optimize resource utilization, ensuring timely and accurate deliveries while enhancing safety and efficiency.

TURNKEY APPLICATION
MIG WELDING

AUTOMATION SOLUTION
PALLETIZING